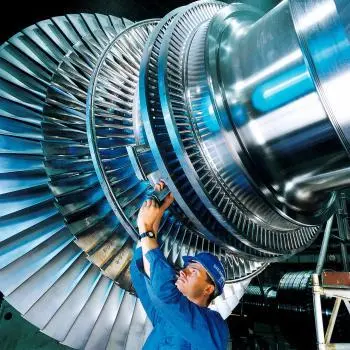
A steam turbine is a machine that exploits the thermal energy of steam at high pressure. This kind of turbine converts thermal energy into useful mechanical energy through an expansion thermodynamic transformation. The steam turbine transforms the internal energy of steam into rotational kinetic energy.
The steam turbine has ultimately prevailed over the steam engine thanks to the best thermal efficiency and the best power/weight ratio.
Maximum efficiency occurs when the steam expansion is an ideal process. In this case, the steam pressure decreases and becomes mechanical work in an infinite number of stages (multi-stage turbine).
One way to classify the different types of turbines is according to their degree of reaction:
-
Action turbines: The expansion is carried out on a fixed set of blades.
-
Reaction turbines: The expansion can be carried out on the fixed blades and the moving turbine blades.
The steam leaves the turbine as a saturated vapor at a lower temperature and pressure than it entered. Afterward, it is sent to the condenser to be cooled.
The modern steam turbine was invented in 1884 by Sir Charles Parsons.
What are the uses of steam turbines?
There are different uses of turbines, depending on how you want to use steam energy.
1. Thermal power plants and electricity generation
Steam turbine generators can produce electrical power, due to the turbine generates rotary motion. Some examples are nuclear power plants, coal-fired power plants (fossil fuel), and some solar thermal power plants.
Together, all thermal power plants generate about 80% of the world’s electricity - in the United States, it is about 85%.
In this case, they work in ideal regimes since the generators have to rotate at a constant speed.
Furthermore, the steam turbine can also function as the motor of an electric generator. The main advantage is that it does not require any mechanical member that transforms the reciprocating movement into a rotary one.
Turbines for electricity production usually couple the turbine shaft to its generator.
As nuclear reactors operate at lower temperatures and with less gas pressure than thermal power plants, they usually run at half the rotation speed.
2. Industrial processes
Another field in which steam turbines are used is in plants such as refineries, paper mills, and other plants where high levels of process steam are required.
The plant can be designed in such a way that it makes use of the steam turbine to obtain a synergy between:
-
Steam production
-
That of electrical energy or mechanical work.
3. Steam turbines for transportation
Steam turbines are also used as marine engines on ships, where the limited dimensions are an advantage. Propulsion steam turbine locomotives were also built, but their diffusion was minimal.
In ships, steam turbine-based propulsion has multiple advantages over internal combustion engines:
-
The smaller size and weight for the same power
-
Less maintenance
-
Fewer vibrations.
However, a steam turbine is only efficient at high rotational speeds. It requires precise and complex transmissions (and at a high cost).
An alternative is the use of turbo-electric propulsion. In this system, the turbines generate electrical energy as in a power plant. The energy obtained is used to electric power motors that drive the propellers.
Basic steam turbine structures
The steam turbine consists of two main parts:
-
The rotor with blades is the moving part of the turbine.
-
The stator with nozzles is a fixed part.
A reaction stage is a row of fixed nozzles followed by a row of moving nozzles.
In the direction of steam flow, axial steam turbines are distinguished. The steam flow moves along the turbine’s axis, and radial, in which the movement of steam flow is perpendicular, and the rotor blades are parallel to the axis of rotation.
According to the number of cylinders, turbines are subdivided into single-cylinder and two-three-four-five-cylinder. The multi-cylinder turbine allows large available thermal enthalpy differences by placing a large number of pressure stages, using high-quality materials in the high-pressure pars, and bifurcating the steam flow in the medium and low-pressure parts. Such a turbine turns out to be more expensive, heavy, and complicated. Therefore, multi-casing turbines are used in powerful steam turbine plants.
According to the number of shafts, single-shaft, double-shaft, less often three-shaft, connected by a typical thermal process or by a standard gear transmission (reducer), are distinguished. The shafts’ arrangement can be either coaxial or parallel - with an independent structure of the shafts’ axes.
A limit regulator (safety regulator) is installed at the shaft’s front end, which automatically stops the turbine when the speed increases by 10-12% above the nominal.
An impulse turbine has fixed nozzles that orient the steam flow into high-speed jets.